Craftsmen in 18th Century Williamsburg
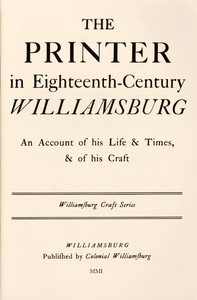
The Printer in Eighteenth-Century Williamsburg by Parke Rouse
The good people of Williamsburg, Virginia, have produced a series of booklets on craftsmen operating there during the 18th Century and generously made them publicly available on Project Gutenberg.
While my site is about 18th Century Britain, the technologies in the Old World and the New would have been much the same. I have extracted some of the more relevant material but I urge you to look at the complete publication. Click on the cover illustration to go to the Gutenberg page.
I have extracted below some notes on 18th century printing techniquest but there is more information at the Gutenberg link.
Techniques of 18th Century Printing
As he received each font or size of type, the colonial printer would distribute it in a set of four wooden trays, two for Roman type and two for italic. These contained partitions for each “character,” or “sort,” as the letters and numerals were called. Such partitions varied in size depending on the frequency of use of each letter or numeral, and they were so placed as to permit the printer to assemble type with a minimum of movement. (Because capital letters are usually arranged in the upper two cases and small letters in the lower two, printers traditionally refer to them as “upper case” or “lower case,” respectively.)
In setting a page of printed matter the colonial printer rapidly plucked the necessary characters, one by one, from their compartments in the upper and lower cases. He placed them, with proper spacing, in a “composing stick” set to the proper length of line. When the stick was full he transferred the type to a shallow wooden tray called a “galley.” Having assembled in the galley enough type to form a page, the printer “tied it off,” i.e., bound a piece of string tightly around the whole mass. Then he could slide the assembled page off the galley onto the surface of the “imposing stone,” a flat marble working surface. Such transfers of type—especially from composing stick to galley—were often attended with accidents. One of the printer’s commoner frustrations was to have a stick, a galley, or even a whole page form of type dropped and “pied.”
On the imposing stone a rectangular wrought-iron frame or “chase” was then placed around the type, and the finished page was locked into place with wooden blocks and wedges called “furniture” and “quoins.” After being locked, it could be picked up and moved to the printing press without danger of the type falling out of place.
The eighteenth-century printer used paper made by hand from linen rags, importing it from Great Britain in the earlier years while domestic mills were gradually developing. Because such paper was uneven in texture and poorly sized, it was dampened before being put on the press to provide a more pliant working surface. For ink, Parks and his contemporaries used a combination of lampblack and varnish, which remain the chief constituents of printer’s ink today. Lampblack was obtained by burning various materials and collecting the carbon in flues, while varnish was made of pine resin boiled in linseed oil until a clear liquid resulted. Most printers “rubbed” or mixed the lampblack and varnish thoroughly. If the mixture was too thick, it could be thinned with linseed oil or whale oil. If red ink was desired for two-color printing, vermilion could be substituted for lampblack.
Once the printer or his apprentices had set the type, pulled a proof, “made up” the type into pages with the proper spacing and ornaments, and then locked it into forms by means of furniture and quoins, he placed his form on the press and adjusted it to get the most even impression. Then he was ready to begin the actual process of printing. Whereas printing is commonly done today by automatic presses, fed with paper either mechanically or by hand, it had to be done one sheet at a time in the eighteenth century. Two men usually worked the press, and the printing of a single impression required approximately a dozen different manual operations.
To ink his press, preparatory to printing, the “beater” spread the necessary amount of ink on his mixing block and rubbed it to an even consistency—that of stiff molasses—with a wooden brayer. With two leather-covered balls attached to wooden handles, he then collected ink from the stone, beat the “ink balls” together to distribute the sticky fluid over their surfaces, and then with a rapid rocking and rolling motion, transferred it onto the type. Then the “puller” placed his paper on a skin-covered wooden frame called a tympan and folded over it another light covered frame, called a frisket. These two frames in turn folded down onto the bed of the press, where the type was locked in its iron form or chase.
The actual impression was made by rolling the bed of the press, complete with folded tympan and frisket, beneath 21 the platen, which was suspended from a large metal screw. By applying the force of the screw, the puller pressed the paper firmly against the inked type. The size of the printed matter might vary from a small bookplate or lottery ticket to a sheet twelve by eighteen inches, which was roughly the page size of Purdie and Dixon’s Virginia Gazette of 1759. Whatever the dimension, the beater had to ink his form and the puller had to close and open his press again each time a surface was printed. Since the platen was so small, only one-half of a two-page wide newspaper could be printed at a time on the early press, and a repeat operation was required to complete one side of the sheet. Thus the press was sometimes called a “two-pull” press.
Two experienced pressmen, working at full speed, could turn out a “token” or 240 printed sheets (with two pulls and on one side only) per hour. Such a speed could not long be maintained; the practical output was closer to 200 sheets per hour. But wages were low, working hours were long, and the printer could keep his force on the job until the work was done.