Craftsmen in 18th Century Williamsburg
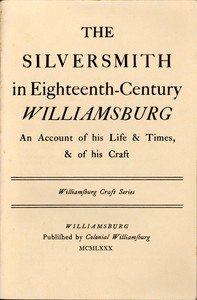
The Silversmith in Eighteenth-Century Williamsburg by Thomas K. Ford and Thomas K. Bullock
The good people of Williamsburg, Virginia, have produced a series of booklets on craftsmen operating there during the 18th Century and generously made them publicly available on Project Gutenberg.
While my site is about 18th Century Britain, the technologies in the Old World and the New would have been much the same. I have extracted some of the more relevant material but I urge you to look at the complete publication. Click on the cover illustration to go to the Gutenberg page.
Of particular interest are the procedures used in the manufacture of silverware.
Procedures used in making silverware
Small items: Casting
If the piece of work to be made was a small ornament, it would be cast directly in a sand mold formed by the smith around a pattern of his own making. The acorn-like finials atop teapots or on the covers of tankards were normally made by casting, often a dozen at a time.
Larger items: Forging, Raising and Seaming
Perhaps, however, some customer ordered a simple, straight-sided silver cup, too large to be cast. Our smith could have made it by any one of three methods and the result would be the same in size, shape, weight, and appearance. Generally only another silversmith could hope to tell which was made by which process: forging, raising, or seaming.
Forging
To forge such a cup the silversmith would have taken a billet of silver perhaps 3/16 inches thick and from it cut a disk of the same diameter as the lip of the finished cup. Then by careful and repeated hammer blows, using shaped anvils of the proper size and curvature, he would pound the metal into the form he required.
Raising
To raise a cup, the smith would start with silver in the form of a flat sheet as thick (or thin) as he wanted the cup to be. He would have made the sheet himself, of course, by beating an ingot to the required thinness. From the sheet he would cut a disk whose diameter equalled the average diameter plus the average height of the finished cup. By carefully hammering the silver just beyond the edge of the anvil, he would force the metal around the outer part of the disk to rise and “shrink” until the cup was shaped.
Seaming
To make a seamed cup the smith would again use thin sheet, cutting from it a small round piece for the bottom of the cup and a slightly curved oblong piece to form its side. He would roll the latter into a somewhat cone-shaped cylinder and solder together the edges. Then he would solder the small disk into the lower end of the cylinder so that the cup was formed. This was by far the quickest and easiest method of making hollow ware. The silversmith’s solder is itself composed predominantly of silver.
Planishing
Whatever method the smith used to form the cup, he would finish it by a process known as planishing. In this procedure the small irregularities in the surface of the piece are carefully hammered smooth by repeated, deft blows of a flat, polished hammer. The face of the planishing anvil is likewise polished to mirror-like smoothness. After planishing would come the filing off of burrs in crevices of the design, and then an all-over polishing with pumice, tripoli, and rouge. At this point the piece would have been ready for surface ornamentation—by engraving, chasing, or repoussé.
Engraving
Engraving means the cutting of a design into the surface of the work; some metal is removed in the process. Chasing is the impression of a design on the surface by the use of appropriately shaped punches. Repoussé consists of raising a design, somewhat like bas relief, by hammering from the back or inside of the work. In the second and third techniques the metal is displaced but not removed.
Stamping
Stamping was normally used only in the forming of such small articles as the bowls of teaspoons. In this procedure a piece of silver was forged to the desired thickness and outline, and placed between a hollowed-out lower die and a rounded upper one. When the smith forced the two dies together by a blow of his heaviest hammer, the bowl of the spoon was formed. By filing, planishing, and polishing—and possibly some engraving—the one-piece spoon was quickly finished.
Combined Techniques
A soup ladle, having a much larger and deeper bowl, would have been formed by the raising process, with the handle made as a separate piece and soldered to the bowl. In fact, only the simplest articles and the smallest ones could be formed by one process alone. The accomplished colonial silversmith had to be able not only to refine and assay his own silver, but to work it up in any combination of techniques that the design made most appropriate.
As an example, the body and spout of a teapot might each have been formed by the seaming process, the base by forging, the top by raising, the finial by casting, and parts of the hinges by drawing. Then all the parts would have been soldered together and the piece planished, polished, and finished off with engraved, chased, or repoussé decoration—or a combination of these. Finally, the smith would have attached a wooden handle, which he might have obtained from a cabinetmaker—or made himself.
Among the silversmith’s final procedures would have been the stamping of his mark, his initials, or his name on the piece. This practice of identifying the maker of an article of gold or silver ware is of long standing, though perhaps not so ancient as the custom by which a painter or sculptor signs his work.